A 10-Day Dash to Build Robots That Fight COVID-19
Mobile Robots Help Disinfect High-Touch Surfaces
At just over three feet (.98 m) tall, the four-wheeled robot may not look like much as it rolls through the office parks of urban Singapore—but don’t let that fool you. Equipped with commercial-grade disinfectant and a double-barreled spray gun, the small robot from Weston Robot is diligently disinfecting any high-touch surface in its path. Whether it is being remotely controlled by personnel offsite or autonomously cruising empty hotel rooms with an infection-zapping UV light, this robot is diligently going where humans no longer should.
Weston Robot designed three new disinfecting and temperature-monitoring robot prototypes. Each took just 10 days.
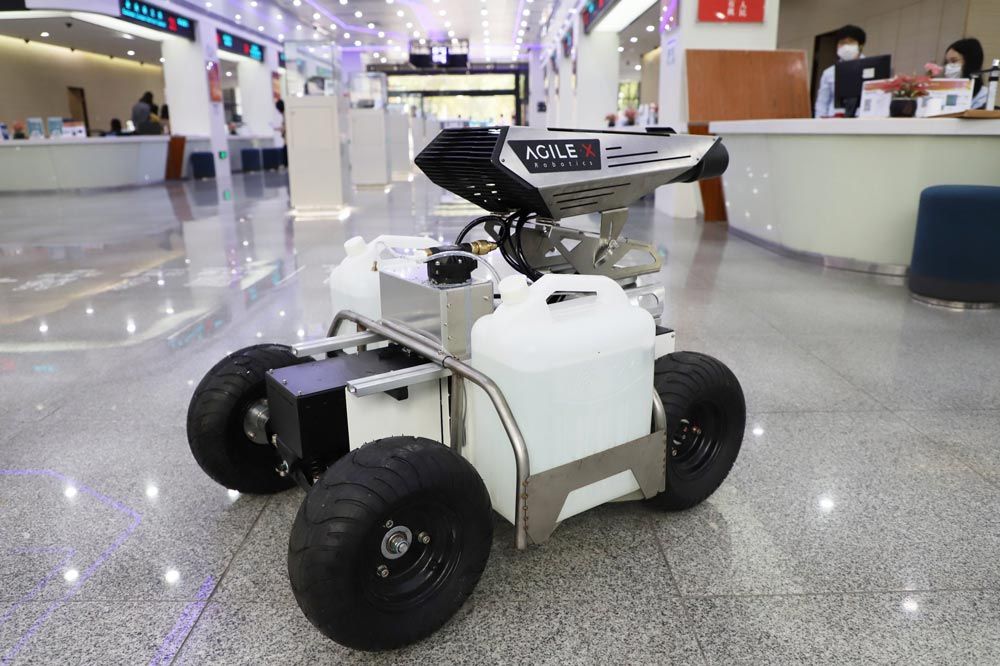
The disinfecting robot designed by Weston Robot and AgileX. Image credit: AgileX
For decades, humans have been dreaming up ways that robots could make their lives easier by taking over high-risk or tedious jobs, but with these disinfecting robots, the dream is more of a necessity.
The global community has been hit hard and fast by COVID-19, an infectious disease caused by a new coronavirus. The illness was classified by the World Health Organization as a pandemic in March 2020, and the virus had infected over 5 million people worldwide as of June 2020. The virus is spread through respiratory droplets, either directly entering the body through touching our noses and mouths or inhaled from residual particles left in the air at distances closer than six feet (1.8 m).
As scientists race to understand and create a vaccine for this virus, prevention has focused on early detection, contact tracing, and diligent disinfecting of surfaces and hands while extremely limiting human contact.
For Dr. Yanliang Zhang, managing director and chief scientist of Weston Robot, a Singapore-based robot developer and supplier, using robots to help meet the disinfecting standards was an obvious choice. Weston Robot designed three new disinfecting and temperature-monitoring robot prototypes. Each took just 10 days.
Right Place at the (Wrong) Time
“The first day that COVID-19 was announced to be infectious in humans, my team came together and said ‘We design robots, is there something we can do to mitigate the spread of the virus?’ ” says Zhang. “Obviously, we could not totally design a new robot model at that time. Instead, we wanted to take advantage of what we have already: mobile robots.”
Prior to the outbreak of COVID-19, Weston Robot already had a small arsenal of mobile robots, including compact surveillance robots with wheels designed for uneven terrain such as outdoor parks. Instead of starting from the ground up designing new robots to combat the virus, the team retrofitted these existing robots with tools for disinfecting.
“We asked ourselves, ‘Can we add something to these robots, for example, a spray gun to spray chemical disinfectant?’ ” says Zhang.
“We saw a lot of demand for robots for disinfection and delivering supplies to combat the spread of the virus.”
Although Weston Robot designs other types of robotic solutions, including autonomous cars and exoskeletons, Zhang says that the team quickly decided that small robots like these would be the best solution. Not only were they easier to retrofit, but they could also help lessen the burden on healthcare and other workers by providing easy-to-control, safe options for disinfection and delivery of essential goods.
“When this happened, we saw a lot of demand for robots for disinfection and delivering supplies to combat the spread of the virus,” says Zhang.
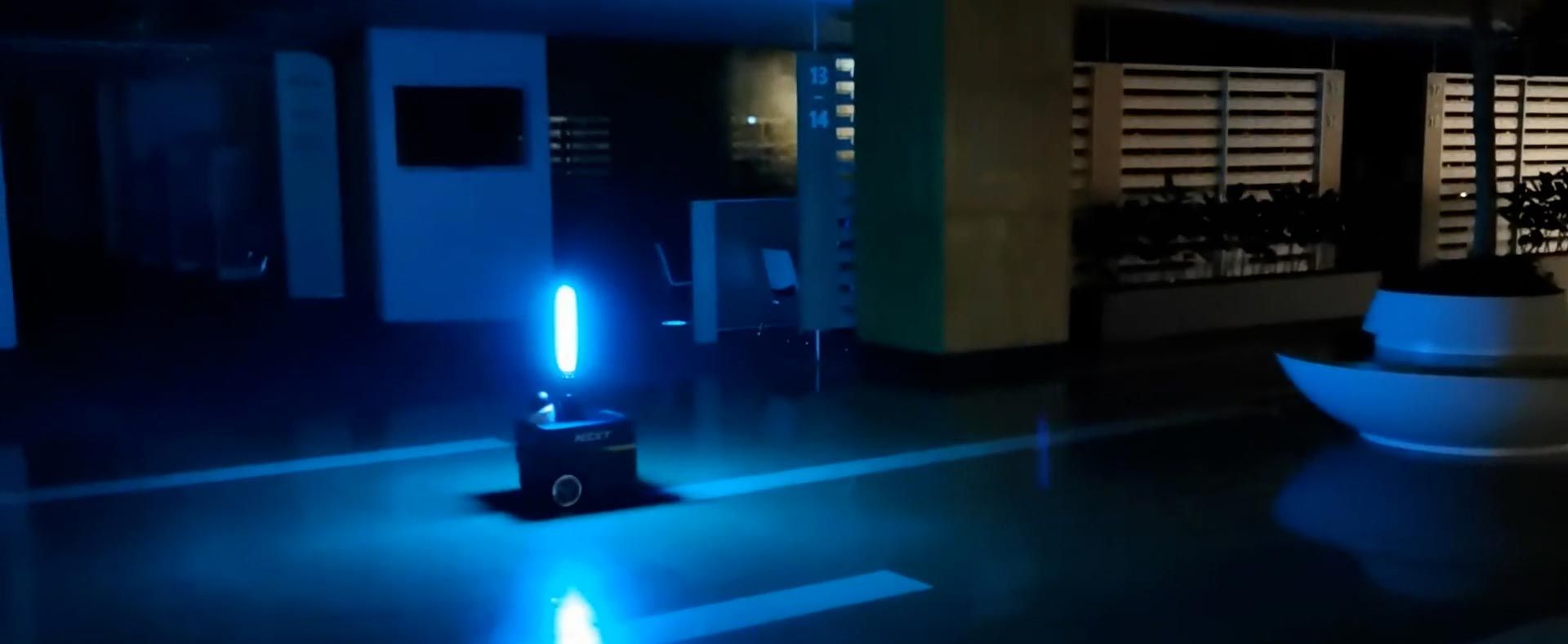
This robot designed by Weston Robot uses a UV light to disinfect building interiors. Image credit: Weston Robot
Unusual Solutions for Unusual Times
But, even with prefabricated mobile robot bodies, creating new prototypes in a matter of days was no small feat. To get the job done, the team relied on quick modeling and simulation using Model-Based Design with MATLAB® and Simulink®. This approach enabled the team to quickly identify and correct emerging problems in their new designs.
“We didn’t want to start from scratch. We searched for different components in the market and integrated and tested the components.”
Another way they sped up their prototyping process was by incorporating ready-made equipment available on the market into their preexisting robots. Zhang says that the initial prototype of their disinfectant-spraying robot used a spray gun designed for washing cars.
“We didn’t want to start from scratch,” says Zhang. “We searched for different components in the market and integrated and tested the components.”
In addition to physically building these robot prototypes, the team also faced a few software challenges—namely, how to effectively communicate with and control these robots to ensure accuracy and safety in the environments where they are deployed.
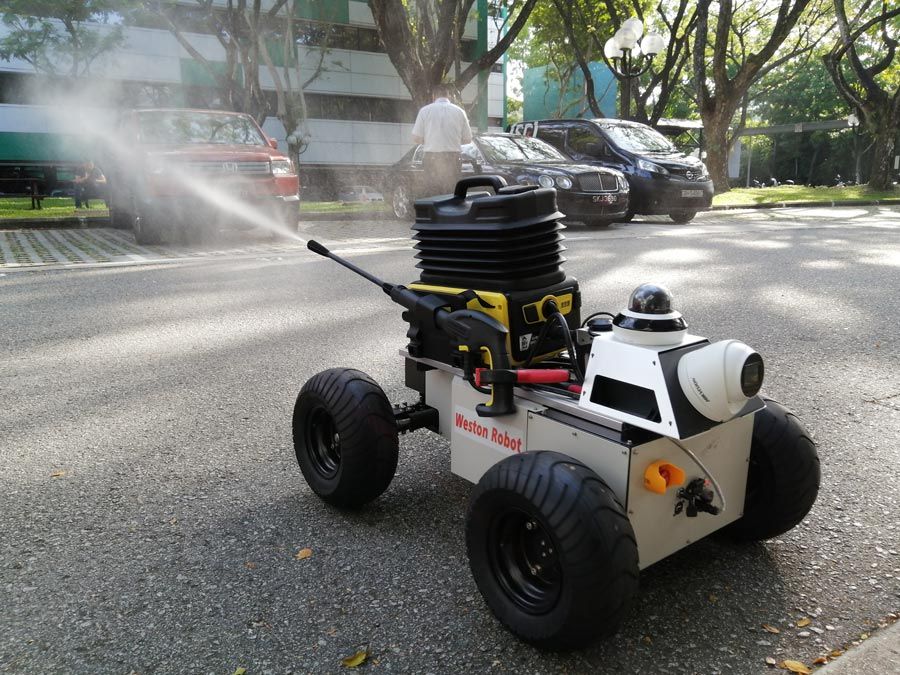
The first prototype of the disinfecting robot. Image credit: Weston Robot
To overcome these design obstacles, the team decided to use 4G to remotely control the robots in less predictable environments, like the outdoor robots that roam through parks. This approach enables them to better control where disinfectants are sprayed and ensure the safety of the robot as well as any human passersby.
In indoor environments, instead of the robot spraying potentially dangerous disinfectants, the team opted for UV lights and preprogrammed autonomous movement maps—similar to how a robot vacuum would move through a map of your living room to clean.
After rigorous prototyping and trial-and-error testing of each idea, the team emerged with three prototypes: an outdoor robot designed to spray chemical disinfectant in environments such as industrial parks and shopping centers, an indoor robot equipped with a UV light column designed to non-invasively disinfect environments such as dorm rooms and hotels, and a hand sanitizer and tissue delivery robot equipped with an infrared camera to take people’s temperatures.
Each robot weighs about 100 pounds (45 kg) and is no taller than 3.3 feet (1 m). The outdoor robot can carry 8 gallons (30 L) of disinfectant and cover nearly 4 acres (14,800 sq m) in a single charge, and the indoor disinfecting robot can cover 10 to 15 rooms with the same amount of charge.
Taking these robots from prototypes to a finished product took another month and was accomplished with the help of Agile X, a mobile robot manufacturing company in China.
“In the final product, we do redevelop everything,” say Zhang. “Agile X is very good at manufacturing hardware, so they can quickly realize your idea and do product assembly testing there. During lockdown it is very difficult for us to get components from the supply chain, but they are very good at making the whole robot given our design specifications.”
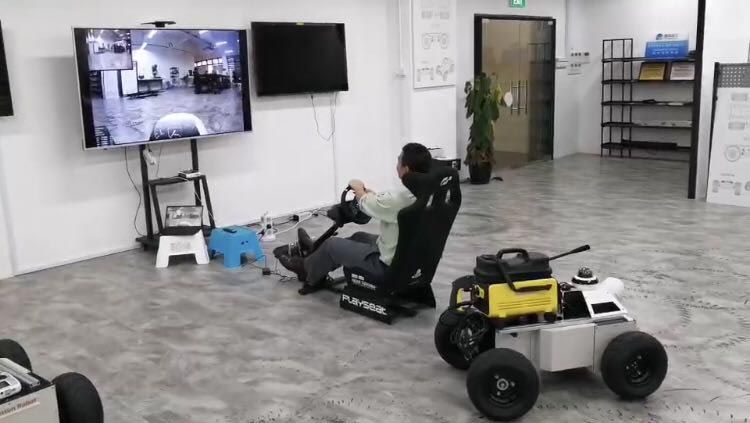
The disinfecting robot can be controlled remotely. Cameras on the robot provide the operator with view of the robot’s surroundings. Image credit: Weston Robot
Preparing for the New Normal
These robots have already begun to roll out in Italy and China, with more expected to be delivered around the world in June. As Weston Robot continues to refine their designs, Zhang says that the team has already begun to learn lessons about what kind of robots the public wants to interact with—and what kind they don’t.
The temperature-monitoring robot wasn’t originally designed to deliver hand sanitizer and tissues, but Zhang says that people found the robot a little too intrusive when it was just a camera.
“People might feel like they’re being monitored all the time,” says Zhang. “So, my team said, ‘Let’s try to make this robot a bit soft.’ For example, we now provide some hand sanitizer and tissue paper with the robot so that people proactively come near the camera and robot. We made the robots more friendly and approachable.”
As these robots continue to be used both through the brunt of the pandemic and afterwards to prevent additional waves of infection, the team wants to ensure that they’re as intuitive to use and easy to interact with as possible. To that end, the team has enabled workers to control them via a computer tablet after a few simple lessons.
Weston Robot is pursuing certifications that will ensure the safety of batteries and other internal components and help make these robots “street legal” in more places across the world. But, those certifications are currently on hold as a result of global lockdowns.
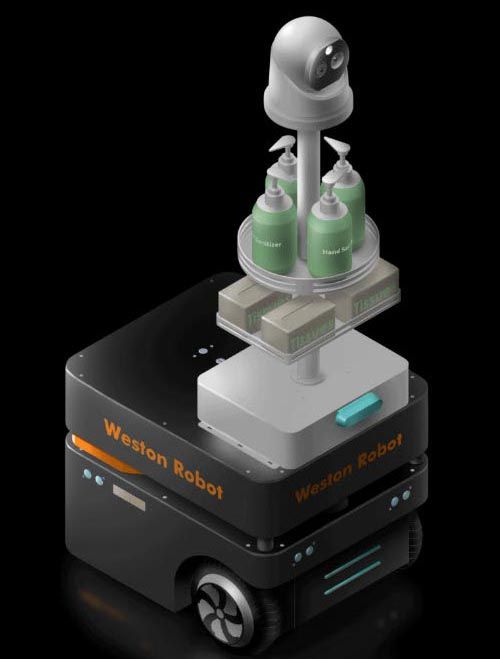
This robot monitors temperatures to detect possible infection. It also offers hand sanitizer and tissues. Image credit: Weston Robot
To ensure that the robots are as intuitive to use and easy to interact with as possible, the team has enabled workers to control them via a computer tablet after a few simple lessons.
“We have to make sure it will pass all the certifications,” says Zhang. “But right now, even the certification center is locked down.”
These certifications are not required during the robots’ trial phase but will be at the top of Weston Robot’s list when countries begin to reopen. Meanwhile, these robots will start their work making sure the “new normal” is as safe as possible.