Cochlear Ltd. Streamlines Development of Cochlear Implant Sound Processing Algorithms
“MATLAB, Simulink, and Simulink Real-Time provide a robust, flexible, and efficient means of integrating the many different technologies that cochlear implants require. We identify the best ideas faster, and our recipients experience the improvements in real-time tests, which are essential to our research.”
Challenge
Solution
Results
- Algorithm development overhead reduced by 60%
- Six times as many new algorithms tested
- Platform integration problems eliminated
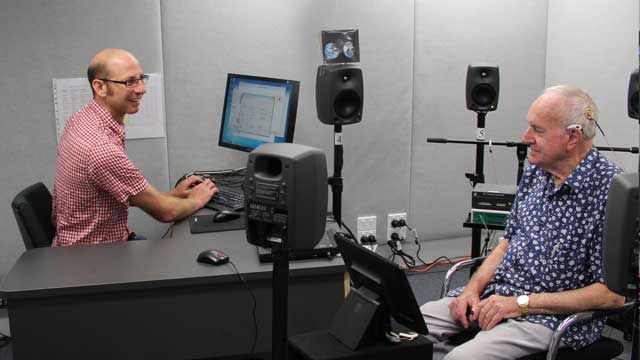
As the global leader in implantable hearing solutions, Cochlear Limited is dedicated to connecting hearing-impaired individuals with the world of sound. There are more than 185,000 Cochlear™ Nucleus® Implant systems registered globally.
The company’s noise reduction algorithms for cochlear implants enhance the ability of the listener to perceive speech in challenging acoustic environments. Cochlear has achieved significant gains in the clinical performance of these algorithms using real-time testing on a rapid prototyping platform developed with MATLAB® and Simulink®.
“With Simulink, engineers and scientists can clearly visualize the integration and operation of new algorithms within the existing commercial signal path,” says Dr. John Heasman, principal engineer at Cochlear. “Our engineers prototype algorithms using Simulink models that are clinically applied using real-time tests with cochlear implant recipients. The ability to create real-time models of algorithms using Simulink Coder and Simulink Real-Time is vital to the success of our research and clinical outcomes.”
Challenge
Cochlear evaluates algorithms developed by external researchers and internal engineering teams. “There is no shortage of great ideas in the field of signal processing for cochlear implants,” says Heasman. “The real challenge is identifying those algorithms that offer the most promise for our cochlear implant population. To do this, we first analyze each algorithm empirically on the bench and develop those offering the most clinical potential.”
The commercially available behind-the-ear (BTE) sound processors of Cochlear implants employ proprietary DSP hardware. Consequently, candidate research algorithms needed to be hand-coded in assembly language before they could be clinically validated in real time with implant recipients. “In the research environment, investing significant time coding algorithms in assembly language represents poor resource utilization,” Heasman explains. “We wanted to circumvent this bottleneck by implementing candidate noise reduction algorithms in real time using a rapid prototyping system rather than coding in a DSP language.”
Solution
The Cochlear R&D group implemented a workflow for evaluating and optimizing noise-reduction algorithms using MATLAB, Simulink, Simulink Coder™, and Simulink Real-Time™.
Engineers used MATLAB and Simulink to model the signal processing path of the company’s commercial products. This baseline model was then used both as a framework and clinical benchmark for the implementation of new algorithms.
Engineers model new ideas in Simulink using fast Fourier transform (FFT), inverse FFT, and other blocks from DSP System Toolbox™ and the Simulink library. The workflow also supports the translation of algorithms, written in MATLAB and other languages by research collaborators, into Simulink models.
The Simulink models are typically built using floating-point blocks. If the engineers suspect fixed-point limitations may impact clinical performance, Fixed-Point Designer™ is employed to convert relevant model components to fixed point prior to simulation.
During simulations, the models are subjected to predefined acoustic test inputs, for which the engineers have already produced a set of desired outputs. The team uses MATLAB to analyze the simulation results and compare them with the desired outputs.
After identifying a promising algorithm, the engineers generate C code from the Simulink model using Simulink Coder. The code is compiled and deployed to a Speedgoat turnkey real-time system with Simulink Real-Time.
In clinical validations, the Simulink Real-Time system is linked via custom hardware to a recipient’s implant, enabling the clinician to measure the clinical performance of the algorithm using simulated real-life acoustic environments, including live speech in quiet and competing noise.
A GUI built in MATLAB enables the clinician or engineer to load clinical settings, select algorithms, and adjust parameters in real time. The recipient has access to a similar interface to rate the performance of each system variation for criteria such as speech clarity and ease of listening.
Results
Algorithm development overhead reduced by 60%. “With Simulink and Simulink Real-Time, we estimate we have achieved a 60% savings in engineering development overhead compared with our previous approach, which relied heavily on assembly language coding,” says Heasman.
Six times as many new algorithms tested. “In the past it could take up to three months to implement a single algorithm on the commercial platform,” says Heasman. “Through Simulink simulations, we can rapidly filter out ideas that we predict won’t work, and then use Simulink Real-Time to conduct real-time tests on six or more algorithms in the time it previously took us to do one.”
Platform integration problems eliminated. “We haven’t had to deal with the integration issues that are common when using disparate technologies,” says Heasman. “Our Simulink signal processing models are tested in real time with Simulink Real-Time, and we close the loop with MATLAB based interfaces that enable clinicians and recipients to control parameters and record the results.”