INTACTON Deploys Sensor with Production Code Generated by Embedded Coder
"Now that we have a complete design and code-generation tool chain based on Simulink and Embedded Coder, most field test changes occur in minutes. This would have been impossible to do using manual approaches."
Challenge
Solution
Results
- Accomplished goals with limited resources
- Met aggressive deadlines
- Reduced code execution time
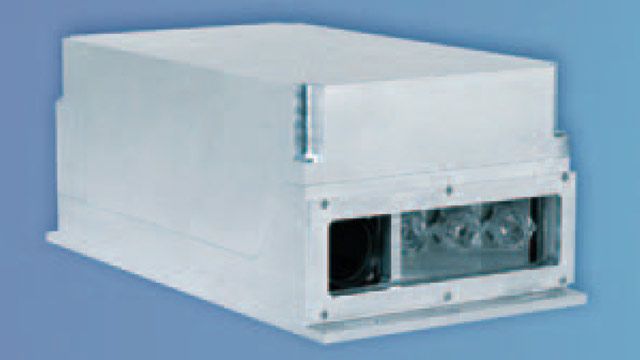
INTACTON develops innovative sensor technologies that enable industrial engineers to optimize product quality and quantity by optically measuring the velocity and length of paper and steel, for example, while they are transported on assembly lines.
Today's optical sensors, however, include technology based on costly, high-maintenance custom devices. To reduce production costs and increase reliability, INTACTON developed an optical sensor based on standard components, including a charge-coupled device (CCD) camera and a Texas Instruments C6000 DSP. Using MathWorks tools for Model-Based Design, they designed the sensor with a small development staff, tight time constraints, and minimal DSP programming experience.
"We needed a complete design and automated implementation environment for embedded systems," explains Arno Bergmann, project manager at INTACTON. "MathWorks tools provided us with a single solution to quickly cycle through design steps of simulation, rapid prototyping, and production code generation."
Challenge
Since no one had produced an optical sensor based on a standard CCD camera and a DSP, INTACTON engineers would need to explore and analyze complete system behavior, including many degrees-of-freedom that account for lighting situations and different surface properties of products.
INTACTON would also need to deliver the product to market ahead of the competition within budget in just 18 months. To meet this deadline, they would need to dedicate most of their time to researching and designing the algorithm behavior—not programming DSPs. Because their development staff had minimal DSP programming and implementation experience, INTACTON would require proven code-generation capabilities.
"To meet our deadline, it was critical for us to focus on exploring the sensor system functionality instead of working on C-code issues," says Bergmann.
Solution
INTACTON implemented a new system development process based on MathWorks tools for Model-Based Design to model, simulate, and automatically generate production code for the sensor within the 18-month deadline.
They created a complete design environment using Simulink for modeling and simulation; DSP System Toolbox™ for FFT design and statistics; Simulink Fixed Point for calculating integer math; and Embedded Coder® for automatic production code generation, rapid prototyping, deployment, and embedded software verification.
To meet their aggressive production schedules and to integrate the generated code into their embedded target, INTACTON worked with The MathWorks in Germany to ramp up quickly on MathWorks tools.
"By working with The MathWorks, we quickly generated code from our models and compiled and downloaded the code onto our target for real-time execution and verification," Bergmann explains.
Using MATLAB and Simulink for offline simulation and data acquisition, INTACTON first conducted a feasibility study to ensure the proper operation of the spatial filter method with their DSP hardware. With this approach, they performed the study in only two months with few hardware components and minimal coding.
Engineers then transitioned to a rapid prototyping phase using Embedded Coder. They used the target to integrate the automatically generated code from Embedded Coder with TI’s operating system software before compiling it with Code Composer Studio. Using Embedded Coder, engineers also accessed TI’s RTDX data interface to verify code accuracy and performance.
"It is very important to verify the accuracy and performance of the generated code as it runs on the target DSP, and to compare the performance with the original design," Bergmann explains. "We verified the real-time performance and accuracy of the generated code directly from MATLAB and Simulink with Embedded Coder."
INTACTON is now deploying the sensor prototype using code generated and integrated by Embedded Coder. They are performing field tests by controlling a cutter in a textile machine that includes acceleration forces of up to 10g.
Results
Accomplished goals with limited resources. "For a staff of six engineers, it would not have been possible to simultaneously develop optics, mechanics, hardware, algorithms, and a DSP implementation," says Bergmann. "MathWorks tools enabled us to accomplish all of our goals."
Met aggressive deadlines. "We needed to demonstrate a working prototype at a major tradeshow," notes Bergmann. "With MathWorks tools, we met this deadline and are ready for our production release soon."
Reduced code execution time. "Because we quickly verified our code, we had more time to optimize the code and incorporate changes based on customer feedback. In one example, we reduced code execution time from more than 200 milliseconds to less than 2 milliseconds," Bergmann explains. "The excellent support and good results we received from The MathWorks certainly helped us."