MBDA Develops Six-Degrees-of-Freedom Motion Test Platform to Demonstrate Tracking Antenna Controller
“Without a real-time platform, we would need costly flight tests to demonstrate our technology to our customer. With Model-Based Design we sped the development of a six-degrees-of-freedom model for real-time, hardware-in-the-loop simulations that increased our customer’s confidence in our technology.”
Challenge
Solution
Results
- Development time halved
- Errors identified and resolved early in development
- Costly flight tests minimized
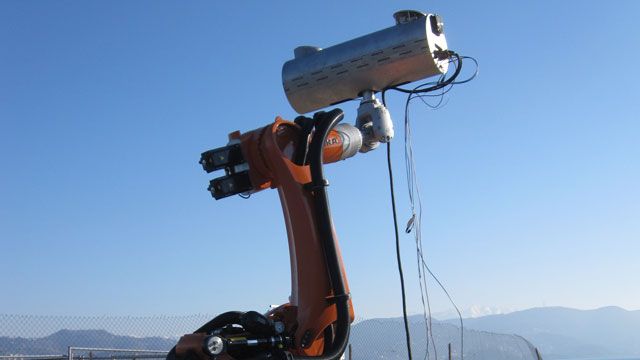
Engineers at MBDA recently created a tracking antenna controller that enables a rocket in flight to communicate to the ground station via satellite. After MBDA successfully demonstrated this technology to its customer in static tests, the customer asked MBDA to demonstrate its operation in a dynamic environment.
To meet this requirement as rapidly as possible, MBDA used Model-Based Design to develop a real-time, six-degrees-of-freedom motion platform. During demonstrations, the tracking antenna controller counteracted the motion of the platform to keep the antenna pointed at the satellite, ensuring reliable communications.
“Our objective was to gain the confidence of our customer by providing a dynamic demonstration of satellite communications in a very short time,” says Tonino Genito, department head at MBDA. “Model-Based Design with MATLAB and Simulink enabled us to rapidly develop a first prototype and speed up the entire process while reducing costs.”
Challenge
In the static demonstration, a rocket platform located in La Spezia communicated via satellite to a ground station 400 km away in Rome. To achieve a milestone for continuing development, MBDA needed to conduct a real-time demonstration in which the attitude of the rocket changed as it would in flight.
On similar projects in the past, MBDA developed numerical simulation systems by hand-coding in C++ or Fortran. The engineers recognized that this approach would be too slow to meet the project’s deadline.
With less than three months to adapt the six-degrees-of-freedom motion platform, the team of just two engineers needed to speed the development of the motion platform and its real-time, hardware-in-the-loop (HIL) simulation system.
Solution
The MBDA engineers used Model-Based Design with MATLAB® and Simulink® to develop the real-time motion platform.
They adapted a six-degrees-of-freedom rocket model that MBDA had previously developed in Simulink. They combined this model with the tracking antenna controller model, which another MBDA team had developed in Simulink. Using the combined model they ran Monte Carlo simulations and refined the system’s accuracy and bandwidth requirements.
The two engineers generated code from the antenna controller model with Simulink Coder™ and used Simulink Real-Time™ to run the code in real time on a dedicated target PC connected to a motion platform actuated by an industrial robot. The antenna was mounted on the platform, and the robot’s motion was based on the results generated by the real-time simulation.
Using this setup, the team conducted real-time HIL tests with the platform and tracking antenna to verify their requirements and the results of earlier simulations.
After conducting further internal tests, MBDA demonstrated that the antenna controller could track a satellite throughout an entire mission simulated on the motion platform while maintaining reliable satellite communications between the test platform and the ground station.
MBDA engineers are currently working on a project that will enable them to test guidance, navigation, and control algorithms on embedded hardware by generating code from Simulink models with Embedded Coder®.
Results
Development time halved. “Compared with our previous approach, in which we wrote code by hand, Model-Based Design reduced development and verification time by about 50%,” says Genito. “Code generation contributed to this time savings, as did the ability to detect problems through simulation and quickly correct them in the model.”
Errors identified and resolved early in development. “Using Model-Based Design we rapidly identified and resolved design errors, converging on zero errors in a very short time,” says Nazario Tancredi, system engineer at MBDA. “With a traditional approach, the probability of finding an error remains consistent throughout the project, but with Model-Based Design it decreases rapidly.”
Costly flight tests minimized. “Because they can be very expensive, we strive to minimize the number of flight tests we need to conduct,” says Genito. “With Model-Based Design, we accelerated the development of a real-time system for HIL tests that enabled us to achieve that goal.”