Research Engineers Advance Control System Design of the International Linear Collider
"Using Parallel Computing Toolbox, we deployed our Simulink model on a large group cluster for distributed execution. We could simultaneously run simulations providing coverage for hundreds of scenarios. As a result, we achieved a linear speedup in the turnaround time for this task. MathWorks tools have enabled us to accomplish work that was once impossible."
Challenge
Solution
Results
- Simulation time reduced by an order of magnitude
- Development integrated
- Existing work leveraged
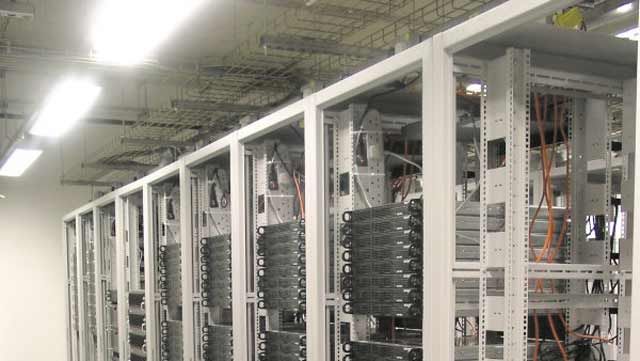
The International Linear Collider (ILC) is expected to enable researchers and particle physicists to answer questions about the origins of mass, the existence of additional dimensions in the universe, and the nature of gravity. Comprised of two linear accelerators, each 20 kilometers long, the ILC accelerates beams of electrons and positrons toward each other to produce collision energies of up to 1000 Giga-electron volts. To ensure the two beams are aligned, the ILC must be designed with extreme accuracy.
The ILC Global Design Effort is driven by the work of hundreds of scientists and engineers at universities and laboratories. As part of that effort, researchers at Queen Mary, University of London are ensuring the effectiveness of the ILC design with MathWorks tools.
"Delivering the particle beam to the interaction point while maintaining a small beam size requires accurate alignment and tuning algorithms in a distributed feedback system," says Glen White, Research Fellow at Queen Mary, University of London. "To track the particle beams as they travel through the accelerator, we use MathWorks tools for designing the control system, modeling the entire ILC, and running thousands of simulations in a distributed computing environment."
Challenge
At less than five-nanometers thick and traveling near the speed of light, the ILC particle beams can become misaligned by even tiny disturbances. Therefore, the ILC must account for the natural movement of the Earth, including seismic events and the tidal pull of the moon, as well as ground motion caused by trains and vehicle traffic.
To ensure the particle beams collide head-on, researchers would need to develop a real-time beam alignment control system. This development effort relies on accurate simulations requiring a comprehensive model of the entire ILC. Each simulation would need to track millions of individual particles through the accelerator, and incorporate the effects of ground motion.
Needing to conduct hundreds of simulations for multiple machine configurations to arrive at an optimal design, the team also sought an easy way to run the simulations in parallel on a computing cluster.
Solution
White and his colleagues used MATLAB® and Simulink® to model and simulate the ILC and its alignment control system. They then used Parallel Computing Toolbox™ to accelerate development by running more than 100 simulations concurrently.
The group first used MATLAB to consolidate existing models of the collider into a single framework. Using Simulink, White then modeled and simulated the beam alignment control system.
To tune the control system and evaluate the ILC design, the group ran complex simulations of the complete system. Each simulation tracks more than 600 particle bunches modeled as 80,000 individual particles as they travel through 20km of accelerator components in both halves of the collider. Simulations, which initially required two or three days to complete, are run to model random accelerator imperfections, different levels of ground motion, and various machine configurations.
White used Parallel Computing Toolbox to obtain results faster by performing more than 100 simulations in parallel on a computer cluster running a Maui scheduler with a portable batch queue system. This resulted in a speed improvement that scaled with the number of processors in use.
Testing the hardware for the feedback systems has begun at the Advanced Test Facility in Japan. During these tests, White used Instrument Control Toolbox™ to control signal generators and acquire beam position and hardware diagnostic information from high-bandwidth Tektronix TDS7154B oscilloscopes. He then used MATLAB to analyze the acquired data and evaluate feedback system hardware. “MATLAB and Instrument Control Toolbox allowed me to control test hardware, acquire data, and analyze results in one tool,” says White.
White used Simulink, Simulink Coder™, and Xilinx® System Generator to model and generate code for a real-time implementation of the beam control system on a Lyrtech board incorporating a Xilinx FPGA and Texas Instruments™ DSP.
Together with other researchers in the Global Design Effort, White is working toward the release of a build blueprint for the ILC.
Results
- Simulation time reduced by an order of magnitude. “Running a single simulation on a high-power PC takes up to three days of processing time,” says White. “We typically need to simulate 100 sets of input parameters per machine configuration to assess its performance. With Parallel Computing Toolbox, we realized a linear speed improvement enabling us to run those 100 simulations in the time it takes to do one. This reduced the simulation time by hundreds of days.”
- Development integrated. “MathWorks tools provide an integrated environment for developing algorithms, acquiring measurements, analyzing data, controlling instruments, and modeling real-time control systems,” says White. “I can reuse algorithms and do not need to learn a separate language.”
- Existing work leveraged. “Using MATLAB and Simulink, we integrated C and C++ components, unifying models together under a common framework,” notes White. “That has been a huge plus in speeding development.”