Sonova Shortens Product Development Time for Hearing Aids and Implants with Model-Based Design
“Across Sonova, engineers from a variety of backgrounds use MATLAB and Simulink as a shared language for designing innovative signal processing systems. Model-Based Design and rapid real-time prototyping enable us to maintain the product development pace that our business demands.”
Challenge
Solution
Results
- Real-time prototypes updated in minutes, not days
- 80% of software libraries reused in platform
- Software quality improved
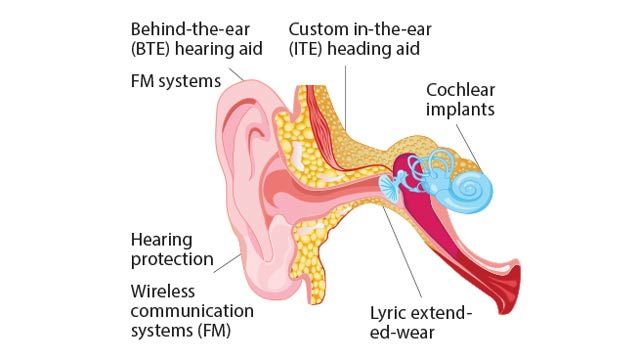
Rapid innovation is a hallmark of the hearing aid and hearing implant industry, and Sonova has consistently generated around 70% of its hearing instrument sales with products that have been on the market for less than two years.
Model-Based Design with MATLAB® and Simulink® helps the company stay ahead of the competition by enabling Sonova engineers to quickly develop new platforms, features, and products.
“With Model-Based Design we can rapidly develop new algorithms, immediately test them on real-time hardware, and reuse them in our platforms across multiple brands and products,” says Raoul Glatt, digital signal processing software manager at Sonova. “MATLAB and Simulink serve as a shared language for Sonova audiologists, signal processing engineers, and acoustics specialists to work together on new features and product ideas.”
Challenge
For a thorough evaluation of a new signal processing feature in a hearing instrument, the system’s output must often be made audible, not just observed on a scope or analyzed numerically and offline.
Sonova needed a way to rapidly translate design ideas into real-time signal processing prototypes that could be wired directly to hearing aid shells containing microphones and speakers. This real-time system would enable audiologists, acoustics specialists, and engineers to assess the truly perceived sound quality, which can be only partially expressed by loudness, sharpness, roughness, pitch, fluctuation strength, and other objective measures.
After identifying promising algorithms via prototyping and implementing them in C, Sonova needed a way to verify the implementations and package them for reuse in their platform and thereby across brand and product lines.
Solution
Sonova adopted MATLAB and Simulink for Model-Based Design to shorten product development times for its hearing instruments and implants.
Engineers explore new signal processing techniques and feature ideas by modeling them in Simulink. Designs are modeled primarily using addition, multiplication, and other basic operation blocks, but some higher-level functions are modeled using DSP System Toolbox™ and embedded MATLAB Function blocks.
After running preliminary simulations in Simulink, the engineers use Simulink Coder™ to generate C code from the model. They compile and deploy this code to a Speedgoat real-time machine running Simulink Real-Time™.
To conduct real-time tests of the prototype, they connect the Speedgoat system’s I/O interfaces to microphones and speakers in a stereolithography hearing aid shell in the acoustic lab. In addition to subjectively evaluating the audio output, the team captures data for postprocessing and analysis using MATLAB and DSP System Toolbox.
After refining the Simulink model based on the results of the real-time tests, engineers use it as a reference to produce highly optimized C code for Sonova’s DSP architecture, a proprietary solution designed to minimize power consumption.
The team developed a MATLAB user interface that integrates the workflows for modeling in Simulink and producing C code. They use this interface to create and execute test vectors that stimulate the model’s inputs and capture its output.
The same tests are ported to C and used to verify the C implementation.
Tested and verified Simulink component models and their corresponding C code become part of a DSP platform library and are available for reuse in product development.
In product development, multiple DSP platform components are integrated to create a full-featured hearing aid or hearing implant. Engineers generate an interactive web view of the corresponding Simulink models with Simulink Report Generator™ for internal customers in other technical units.
Engineering teams throughout the company use these reusable components to assemble complete hearing instrument signal processing systems. Like the individual C libraries, the complete integrated C code is also tested and verified using the MATLAB user interface.
Results
Real-time prototypes updated in minutes, not days. “We can iterate our design in Simulink, regenerate code with Simulink Coder, and be ready to conduct real-time tests with Simulink Real-Time in minutes,” says Glatt. “Without Model-Based Design, each improvement step on real-time hardware would typically take days.”
80% of software libraries reused in platform. “Approximately 80% of the libraries we develop with Simulink are reused in every product we build,” notes Glatt. “We bind our Simulink reference models with our C code, so what we see in our Simulink library is what we get from the C library. Development time for new products is shortened because we are reusing optimized, tested, and verified building blocks.”
Software quality improved. “Within Sonova, engineering teams using Model-Based Design have a lower rate of software defects per new signal processing feature,” says Glatt. “Higher-quality software is key to increasing the rapid rate of innovation and the success of our entire company.”