Argonne National Laboratory Develops Powertrain System Analysis Toolkit
"We developed an advanced vehicle framework and scalable powertrain components in Simulink, designed controllers with Stateflow, automated the assembly of models with MATLAB scripts, and then distributed the complex simulation runs on a computing cluster—all within a single environment."
Challenge
Solution
Use MathWorks tools to model advanced vehicle powertrains and accelerate the simulation of hundreds of vehicle configurations
Results
- Distributed simulation environment developed in an hour
- Simulation time reduced from two weeks to one day
- Simulation results validated using vehicle test data
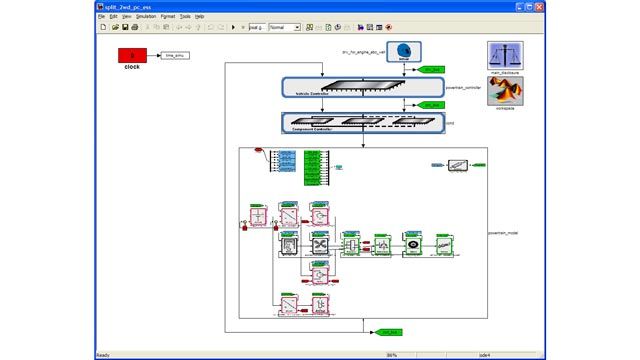
Engineers building next-generation fuel cell, hybrid electric, and plug-in hybrid electric vehicles must optimize fuel economy and performance while containing development costs. To meet these goals, they need to simulate multiple powertrain configurations without building costly physical prototypes.
In response to this need, Argonne National Laboratory (Argonne) collaborated with leading auto-makers to develop the Powertrain System Analysis Toolkit © (PSAT), an automotive engineering tool that evaluates a vehicle's fuel economy and performance by simulating its transient behavior and control system characteristics. The U.S. Department of Energy (DOE) Vehicle Technologies Program funded the development of PSAT and uses PSAT as its primary vehicle simulation tool for all FreedomCAR and 21st Century Truck Partnership activities.
Using Simulink® and other MathWorks products, Argonne researchers not only developed PSAT; they also distributed the many complex simulations needed to evaluate vehicle performance in a multiprocessor environment. Distributing the hundreds of simulations required for each vehicle enabled them to get results much more quickly.
Challenge
DOE studies frequently include up to 800 vehicles that employ a wide range of technologies. Evaluating just one vehicle involves a complex set of variables, technologies, and performance metrics, including driving cycle, fuel economy, and range (for plug-in vehicles).
Argonne researchers needed a flexible modeling and simulation environment that would enable PSAT to support a wide range of technologies. "We wanted a design that would make it easy to plug in new technologies," notes Argonne researcher Sylvain Pagerit. "For example, changing an engine had to be simple."
The group also needed to automate the many complex simulations required for each study.
Solution
Argonne researchers used MathWorks tools to develop the PSAT platform and accelerate the analysis of powertrain configurations.
"We developed an advanced vehicle framework and scalable powertrain components in Simulink, designed controllers with Stateflow®, automated the assembly of models with MATLAB® scripts, and then distributed the complex simulation runs on a computing cluster," says Pagerit.
Working in Simulink, Pagerit and his colleagues created a vehicle framework based on bond-graph, which captured the energy flows around the system. They then developed models for a wide range of powertrain components, including the fuel cell, engine, electric machine, and battery.
Using Stateflow, the team developed control systems to optimize fuel efficiency and balance power use in hybrid vehicles from the combustion engine and electric motor.
Argonne engineers developed algorithms in MATLAB® that generated Simulink models from the framework and powertrain components, automating the creation of vehicle models based on each study’s requirements. For example, for a DOE study Argonne used the MATLAB scripts to generate models for 780 vehicle configurations and to automatically scale battery size, engine power, and other powertrain component parameters.
Working in Simulink, the team optimized fuel economy using the DIviding RECTangle (DIRECT) optimization technique, which required at least 30 iterations and 400 simulations per vehicle.
To reduce simulation time, the Argonne team used MathWorks tools to run PSAT simulations in parallel on a computer cluster with 16 worker nodes. Using Parallel Computing Toolbox™, they set up their simulations to be executed by MATLAB Distributed Computing Server™ workers running on the computer cluster.
Argonne plans to expand the cluster to 32 worker nodes to handle the increasing number of studies with even larger data sets requested by the DOE.
Results
Distributed simulation environment developed in an hour. "It took us about an hour to move our simulations from a single processor to a distributed, 16-node cluster," explains Pagerit.
Simulation time reduced from two weeks to one day. "Using distributed computing, we went from running one set of simulations in two weeks to only one day," says Pagerit. "The speed increase was proportional to the number of processors that we used."
Simulation results validated using vehicle test data. "We have tested existing vehicles, including most of the new hybrids, so we can validate our simulation results against actual measured data," Pagerit says. "All the advanced hybrid vehicles that we have evaluated with PSAT have been accurate to within 5% of the actual fuel economy and battery state-of-charge measurements."