Bell Helicopter Develops World’s First Commercial Fly-by-Wire Helicopter
“With Model-Based Design we had a successful first flight; there were no issues from a control or integration standpoint. Generating the control law code from our Simulink model with Embedded Coder eliminated the slowdowns caused by manual code generation and freed the team to work on meeting the broader program goals.”
Challenge
Solution
Results
- Integration time cut by 90%
- Development iterations reduced from weeks to hours
- Confidence in code quality maintained
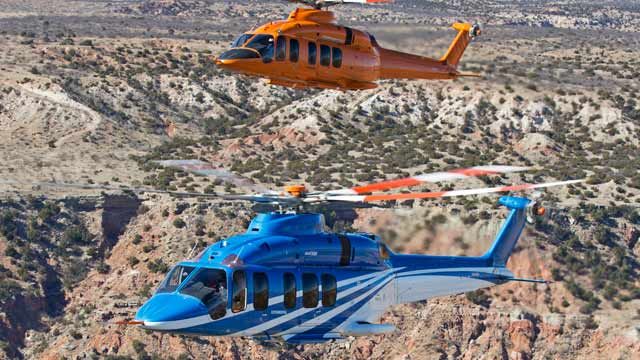
The Bell 525 Relentless is the world’s first commercial helicopter with fly-by-wire flight controls. The fly-by-wire system places the helicopter under full-time computer control, maximizing safety by reducing pilot workload, increasing pilot situational awareness, and improving aircraft handling qualities.
Bell Helicopter used Model-Based Design to develop and implement the control laws for the Bell 525 fly-by-wire system. The project was the first time Bell Helicopter engineers used automatic code generation for a DO-178B Level A workflow.
“We did all the design and extensive simulations in Simulink,” says Mike Bothwell, Bell 525 fly-by-wire control law lead. “The first time we generated code for the real flight control computers with Embedded Coder, we had no integration problems. That was a big deal because, on previous projects, integration problems really slowed us down.”
Challenge
For Bell, being the first to market with a civilian helicopter equipped with fly-by-wire flight controls meant speeding up the slower aspects of its DO-178B software development process by reducing both manual coding and manual code reviews. On past programs, a small manually coded design change would lead to a detailed review process that took too long to support an aggressive flight test development program.
The Bell 525 engineering team wanted to capture improvements over their previous DO-178B development approach. First, they sought to reduce the rework that resulted from manually coding the software requirements. Second, they wanted to streamline the steps needed to integrate code with the rest of the aircraft systems. Third, they wanted to establish a robust development process so that engineers could provide consistent results to other teams and projects.
Solution
Bell Helicopter engineers designed, implemented, and verified the control laws for the Bell 525 fly-by-wire system using Model-Based Design.
Working in Simulink® and Stateflow®, the Flying Qualities Engineers developed a control law model based on 900 high-level system requirements defined in IBM® Rational® DOORS®. The model was partitioned into modules that included pitch, roll, and yaw axes, as well as a logic and mode switching module developed with Stateflow.
They developed a set of test cases and ran simulations in Simulink to verify logic and functionality.
Using Requirements Toolbox™, the engineers linked the requirement definitions in DOORS with the Simulink and Stateflow objects they had used to model the requirements. This traceability enabled the team to perform an impact analysis to identify areas of the Simulink model that would be affected if requirements were updated later in the project.
They also used Simulink Check™ and Simulink Coverage™ to check the modules for compliance with Bell Helicopter modeling standards for DO-178 and to measure model coverage for the test cases. While the coverage analysis is not required for certification credit, it plays a part in the certification process because it helps the team trace low-level tests to high-level requirements.
The team used Simulink Report Generator™ to generate design and requirements tracing reports that can be used for guidance during the review process required for certification.
The engineers generated about 16,000 lines of C code from their Simulink control law model using Embedded Coder®.
By using Simulink Code Inspector™ and qualifying it with DO Qualification Kit, the team ran automated comparisons of the generated code and the control law model to check for unsupported blocks, verify traceability, and satisfy DO-178B code-review objectives.
After code review, the code was compiled and tested using the same test cases as the Simulink model. The software team then integrated the control law code with the other flight control code in preparation for “live” system testing.
The Bell 525 Relentless had a successful first flight and the helicopter is undergoing flight test development to its full speed, weight, and altitude capability. Bell Helicopter is expanding its use of Model-Based Design to future DO-178C projects.
Results
Integration time cut by 90%. “The first time we generated code that was run on real hardware we had no integration issues,” says Bothwell. “In the past, it took about 10 weeks to complete initial integration, but with Model-Based Design we were done in one.”
Development iterations reduced from weeks to hours. “On past programs, when we made a small design change we sometimes had to wait weeks for the software team to code it,” says Jillian Alfred, Bell 525 fly-by-wire control law designer. “With Simulink and Embedded Coder we simply made the change and regenerated the code. We had a new test build within an hour.”
Confidence in code quality maintained. “Model-Based Design enabled us to shorten the duration of time-consuming tasks without compromising the quality of our work,” says Alfred. “We have the same high level of confidence in the quality of the generated code as in the code created using our traditional manual processes. With Embedded Coder we know we are generating the right code, and with Simulink Code Inspector we can guarantee that it is traceable to the model.”