Zühlke Develops High-Vacuum Pressure Sensor Using Model-Based Design
"Model-Based Design with MathWorks tools closes the gap between algorithm development and implementation on target hardware. System modeling and production implementation are merged at a high level of abstraction, which enables us to focus on what is important: the comprehensive analysis and design of an efficient, high-quality product."
Challenge
Solution
Results
- Late change implemented in hours
- Efficient, accurate code generated
- Development time shortened and project risk reduced
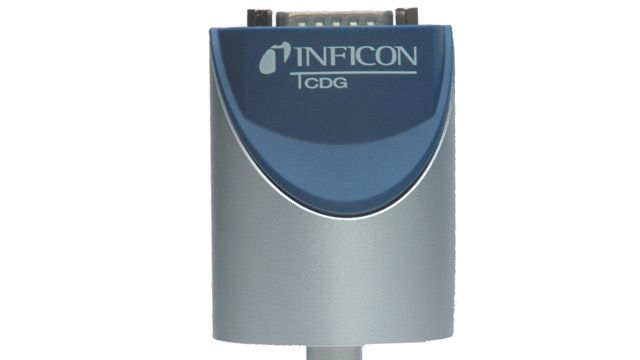
High-vacuum pressure sensors, used in the manufacture of semiconductors, data storage hardware, and video displays, require sensors capable of controlling the vacuum and detecting system failure within milliseconds. To achieve this level of precision, engineers use capacitance diaphragm gauge manometers, sensors that monitor the effects of pressure changes on a thin ceramic membrane. Extremely sensitive to temperature, these devices require complex and lengthy calibration before they can be used in production.
Zühlke developed capacitance diaphragm gauge manometer firmware for INFICON, a leading supplier of vacuum gauges. Using MathWorks tools and Model-Based Design, Zühlke quickly designed and implemented algorithms for temperature compensation, signal linearity, and signal resolution.
"With MathWorks tools, we delivered a system that fully satisfied the needs of our customer and the high-quality demands of the pressure sensor," says Peter Wehrli, Senior Engineer at Zühlke. "The result underscores our ability to leverage Model-Based Design even for projects that do not involve sophisticated target hardware or complex designs."
Challenge
Changes to the shape of the membrane inside the sensor are quantified by measuring the capacitance across two electrodes attached to the membrane's metallic coating. The full range of the most sensitive pressure sensor is 100 millitorr, less than two ten-thousandths of an atmosphere, with a resolution of 3 microtorr.
To achieve this resolution, the sensor firmware would need to convert input capacitance measurements on the order of picofarads. It would also need to calculate pressure while compensating for temperature, ambient pressure, and the effect of gravity on the membrane.
The firmware would be implemented on the 8051-based Analog Devices® microcontroller. At the outset, the team was not sure whether the 8-bit arithmetic capabilities and clock speed of this microprocessor could meet the precision and response time requirements of the sensor. Additionally, while the firmware would ultimately enable technicians to calibrate the sensor by setting parameters in software, Zühlke would not have access to sensor hardware until almost three months into the project.
Solution
Using MathWorks tools and Model-Based Design, Zühlke engineers designed, optimized, and simulated a model of the pressure sensor and then generated production code for the sensor firmware.
The team designed and modeled the sensor system in Simulink, using Stateflow to implement the state machine for the calibration procedure, which is controlled via an RS232 interface. Using Fixed-Point Designer™, the engineers simulated and verified their fixed-point arithmetic computations.
After simulating and debugging the model, the team automatically generated fixed-point C code for the 8051 using Simulink Coder™ and Embedded Coder®.
Zühlke delivered a first version of the system to INFICON engineers, who tested the firmware and provided real-world measurements, including actual pressure readings and sensor output. Zühlke incorporated this data into their Simulink models and used it to tune parameters and optimize the sensor's accuracy.
INFICON incorporated the automatically generated code into its capacitance diaphragm gauge manometer, and has since adapted and reused the model for a new line of sensors and an alternate microprocessor.
Results
- Late change implemented in hours. "When we had almost completed the project, our customer replaced a custom measuring device with an off-the-shelf component that had a completely new interface," says Wehrli. "Using MathWorks tools and Model-Based Design, we implemented changes in the signal processing in half a day that otherwise would have taken us two weeks."
- Efficient, accurate code generated. "The automatically generated code was efficient, enabling us to meet the response time requirements of the specification," says Wehrli. "In addition, the errors we found were in the model, not in the generated code, so in the end our customer saw fewer implementation errors."
- Development time shortened and project risk reduced. "MathWorks tools and Model-Based Design enabled us to reduce risk by finding errors during simulation instead of at production," Wehrli says. "We shortened development times considerably, gained a better understanding of the system, and have graphical documentation of the software that is intuitive and user-independent."