三菱重工开发机械臂以取出核燃料碎片
“使用 MATLAB 和 Simulink 进行基于模型的设计,支持从传统控制到现代控制的多种选择,使其能够轻松响应设计约束的任何变化,满足对机器人的苛刻精度要求。”
挑战
设计一款多轴机器人,用来取出福岛第一核电站的熔毁燃料碎片
解决方案
使用 MATLAB 和 Simulink 执行硬件测量测试,对各个机器人轴和控制器进行建模和仿真
结果
- 开发时间缩短一半
- 超出定位精度要求
- 建立了跨组织协作共享平台
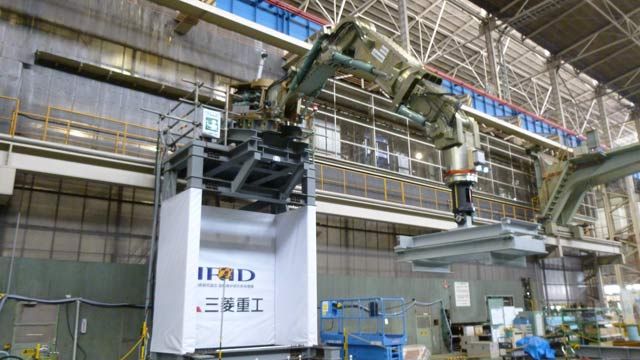
图为三菱重工七米长的机械臂,可承受高达 2000 公斤的处理反作用力。
在福岛第一核电站发生事故后,日本政府开始了长达数年的努力来稳定该核电站并将其退役。这项工作部分由日本国际核退役研究所 (IRID) 负责,它面临的最大技术挑战之一是安全地取出熔毁燃料碎片和内部熔炉结构。
为了取出碎片,三菱重工 (MHI) 正在建造一条 7 米长的机械臂,可承受高达 2000 公斤的处理反作用力。该机器人的液压控制系统使用 Simulink® 设计和验证,可以移动机械臂的六个轴,末端的定位精度仅为 5 毫米,完全在 IRID 要求的 10 毫米内。
三菱重工工程师 Tadashi Murata 表示:“不采用基于模型的设计的话,进行这样的项目通常需要反复试错,从而导致在成本和时间压力下执行重要的重构工作。在项目初始阶段使用 MATLAB 和 Simulink 让我们尽早发现了问题。因此,我们能够将开发和实际设备的调试时间缩短一半。”
挑战
自核电站建成以来,站内的情况发生了重大变化。由于缺乏对实际情况的了解,很难制定机械臂规格。而且因为设计限制在一开始并不明确,三菱重工团队需要运行大量的仿真和硬件在环 (HIL) 测试以改进和验证控制设计。
无论是机器人的尺寸,还是为机械臂设计的液压驱动系统,在三菱重工都是史无前例的。施工现场的挖掘机臂有四个轴(一个旋转轴和三个弯曲轴),机械臂有六个轴(三个旋转轴和三个弯曲轴),以便使末端的定位距离目标不超过 10 毫米。机器人的超大尺寸和液压配置,再加上在此类设备上测试未经充分验证的控制算法所带来的风险,凸显了对控制设计进行大量建模和仿真的需要。
解决方案
三菱重工工程师使用 MATLAB® 和 Simulink 进行基于模型的设计,开发并验证了机械臂的控制软件。
在根据需求规范制定设计大纲后,三菱重工团队对旋转轴和弯曲轴进行了硬件测试,测量了非线性、响应性和摩擦阻力的影响等因素。为了实现这些测量的自动化,该团队使用 MATLAB、Simulink 和实时 Linux® 平台开发了一个测试控制系统。
该团队根据硬件测试期间收集的测量数据,使用 Simulink 建立了一个单轴模型,其中包括液压缸和伺服阀。
此外,他们还使用 Simulink 和 Control System Toolbox™ 开发了一个二自由度 PID 控制模型。该模型结合了液压控制技术(如差压反馈),以及机器人控制技术(如重力补偿)。
他们在 Simulink 中进行仿真以调整控制器增益,确定保持位置所需的扭矩,并检查重力补偿算法的实现情况。
在这些仿真之后,该团队在 Gazebo 中构建了完整的机器人模型,并进行了 HIL 测试。Gazebo 机器人模型和 Simulink 控制器模型通过 ROS 连接。接下来,他们对机器人进行了全面的功能测试,验证了机器人的可移动范围、定位精度和挖掘能力,并使用 MATLAB 对测试结果进行分析。
该项目的目标是按计划开始在福岛进行燃料提取工作。三菱重工计划在未来需要高精度定位和承载重负荷能力的液压机械手上重复使用这些模型和仿真。
结果
- 开发时间缩短一半。Murata 表示:“为了满足国家路线图规定的燃料提取的最后期限,控制开发计划设定为 6 个月,我们最初认为这个时间表太紧了。事实上,借助基于模型的设计,我们将开发时间缩短到了短短 3 个月。”
- 超出定位精度要求。Murata 表示:“我们的系统必须具有高精确度,要求是在载荷为 500 公斤的情况下,将末端定位在 10 毫米以内。 我们在 Simulink 中进行的仿真和测试让我们超越了这个目标,达到了 5 毫米的精度。”
- 建立了跨组织协作共享平台。Murata 表示:“在项目期间,我们咨询了大阪大学的一个研究小组,并收到了宝贵的意见。在讨论控制设计时,使用 Simulink 作为我们共同的语言,使我们所有人都能迅速对算法和设计形成共识。”