Undergraduate Engineers Develop Hydraulic Servo Control Systems Using Model-Based Design with Simulink
By Charles Birdsong Ph.D., California Polytechnic State Univesity at San Luis Obispo
In the past, control engineering was the exclusive province of computer and electrical engineers with advanced degrees and years of experience in low-level programming languages. Today, engineers and students alike can use Model-Based Design to rapidly design and implement real-time control systems without having to learn low-level programming. Used throughout the automotive and aerospace industries, Model-Based Design places a high-level system model at the center of development. This approach helps engineering students understand not only the basic physics of system components, but also the interaction between components and the behavior of the overall system.
Model-Based Design with Simulink® and Simulink Desktop Real-Time™ has changed the way we teach mechanical controls at California Polytechnic State University (Cal Poly) San Luis Obispo. In ME 422 - Mechanical Controls, a fast-paced introduction to control theory required of all seniors in the Mechanical Engineering department, students use MATLAB® and Simulink to process lab data and model and simulate open- and closed-loop systems. Because they have used the MATLAB environment throughout their undergraduate studies, they hit the ground running in the course labs. Most important, Simulink and Simulink Desktop Real-Time enable them to connect control design theory with practical implementation by rapidly implementing a real-time controller prototype.
Course Overview
Mechanical Controls consists of three one-hour lectures and one three-hour lab per week. Topics covered include single-input, single-output linear system modeling, time-domain analysis, transfer functions, root locus, frequency response methods, and proportional integral derivative (PID) and lead lag controllers.
Four lab experiments reinforce the topics covered in lecture. In the first three labs, students explore an analog DC servo position control, a two-tank water-level regulator, and a hydraulic servo control. Each lab experiment is completed in two consecutive weeks.
The final lab is a controller design project that gives the students the opportunity to apply the technical experience and background they have gained throughout the course. Unlike the preceding labs, in which students have a full week between sessions to develop a controller, in the final lab the design is completed in a single session.
Lab Workflow
Each of the first three labs follows the same basic steps: system identification, system analysis, modeling, and simulation. The students measure the behavior of the system in open loop using a National Instruments PCI MIO 16E-4 data acquisition board to record system output for a range of input values. Their assignment is to use this system identification data to design a controller using classical methods—typically, root locus techniques.
Working in MATLAB, the students post-process the data by plotting the waveforms, calculating time constants, and so on. They then build and simulate an open-loop model of the system in Simulink. After comparing their simulation results with the real-world measurements, they build a closed-loop model of the system and test its performance through simulation. This approach reinforces both the importance of classic control theory techniques and the value of simulating a closed-loop system to ensure that it is stable and safe before implementation.
The students submit a report for each lab, typically documenting their results with graphs and plots produced in MATLAB.
Implementing a Hydraulic Servo Control
In the third lab and the final design project, students explore hydraulic servo control systems similar to those used in the construction, manufacturing, and aerospace industries (Figure 1). Our lab room has a hydraulic servo control system consisting of a lead mass mounted on a linear bearing and driven by a hydraulic double-ended cylinder. In previous years, students used a graphical programming environment to complete the lab assignment. To improve the lab, I needed an environment that could provide more accurate integral and derivative control with higher sampling rates and lower latencies in the software.
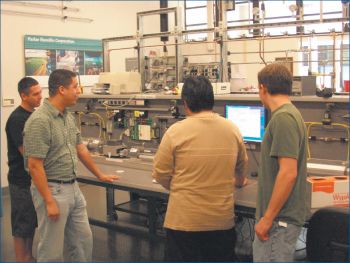
Today, students implement the hydraulic servo control using Simulink and Real-Time Windows Target. By this stage in the course, they are adept at using Simulink to create system models of controllers using feedback, gains, and input sources, and can understand how a control system works by simply looking at the Simulink model (Figure 2).
A primary advantage of switching to Simulink for this lab is that students can follow the same workflow that they used in earlier labs but can now modify the control algorithms themselves, generate code with Simulink Coder®, and then run the system in real time using Simulink Desktop Real-Time. In previous years, students were limited to proportional-only designs, but with Simulink and Simulink Desktop Real-Time, they can build real-time implementations of any type of control, including proportional-only, proportional plus integral, and full PID.
Simulink scopes make it easy for students to analyze signals and answer key questions about their controller’s performance. When asked if a particular actuation signal has saturated, for example, the student can use Simulink to visualize that signal immediately. It is much more difficult to answer this question if the embedded system does not provide access to internal signals.
Using Model-Based Design in the Lab
In the final lab assignment, the students design their own controllers. They use the hydraulic system that they analyzed in the previous lab, but I change its mass and add a damping spring to alter its dynamics.
I perform the system identification by measuring the system’s open-loop frequency response using a signal analyzer. Starting with this frequency response data, the students estimate the transfer function of the system using curve-fitting techniques in MATLAB. They then have about two hours to design a PID controller in Simulink. I give them the option of using either traditional root locus techniques or the SISO design tool in Control System Toolbox™.
I always make sure that the students have learned to draw a root locus by hand before I introduce the SISO design tool. After students see how easy it is to perform root locus analysis with the SISO tool, they’re less interested in the traditional techniques. Nevertheless, the SISO tool is a powerful instructional aid. In the lecture, I can use it to show the root locus on one side of the screen and the step response on the other. When I move the poles around on the root locus, I can see that for the first time, the students really understand the connection between the frequency domain and the time domain for different control designs.
In the final hour of the lab, they use Simulink Desktop Real-Time to implement the designs and evaluate the real-time performance of each controller.
While the course emphasizes the value of iterating their designs, lab time is expensive, and so students are allowed only two tries. They typically find that their first design doesn’t work the way they thought it would, due to the limitations of the model or to design errors. They use their initial results and guidance from me to make design improvements. We evaluate the real-time performance of each controller by plotting the desired profile against the measured profile (Figure 3).
The student with the best performing controller (lowest root mean square error) wins extra credit.
This kind of lab experience, in which multiple teams of students design control systems, observe their real-time implementations, make modifications, and re-test—all in a single three-hour lab session—would not be possible without Model-Based Design and the rapid prototyping capabilities of Simulink and Simulink Desktop Real-Time.
From a teaching standpoint, being able to show the students their controller design working on actual hardware helps me demonstrate the relevance of control theory. Without that real-world experience, the course material can seem academic and theoretical, but once they have seen their own controller moving a mass back and forth, none of the students ever again says, “I don’t see the point of control theory.”
Published 2009 - 91585v00