Océ Technologies Develops Perfect Axial Registration for Direct Imaging
"Using MathWorks products, we speeded up the development of a functional prototype that enabled us to prove the feasibility of Perfect Axial Registration."
Challenge
Solution
Results
- Development time cut in half
- Efficiency increased through model reuse
- Learning curve shortened
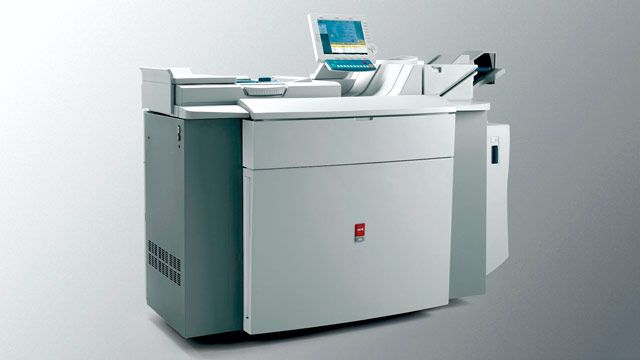
Océ, one of the world's leading suppliers of products and services for professional printing and document management, has developed an innovative color technology that enables a reliable, productive printing system with consistent quality. The Océ CPS700 was the first system using this Direct Imaging technology. It is also the basis of the improved and recently introduced Océ CPS800 and Océ CPS900 systems. Within the research and development department, the feasibility of Perfect Axial Registration for Direct Imaging was demonstrated.
Direct Imaging technology uses seven direct imaging drums with 8,000 electrical conductive tracks on which a monocolor dry toner image is generated by drivers inside the drums. An intermediate drum with a circumference of almost one meter gathers all seven partial images and transfers them in a single pass onto paper, creating the full image.
A small team led by René van der Meer, an Océ researcher dedicated to continuously improving this technology, used MathWorks products at Océ’s largest research and development site in Venlo, the Netherlands to prove the feasibility of Perfect Axial Registration in aligning all seven drums during the printing process.
"In just six months, MathWorks tools enabled us to complete a fast, flexible implementation of a Perfect Axial Registration system with low overhead and minimal low-level coding," says Van der Meer.
Challenge
Perfect Axial Registration requires all 56,000 tracks (7x8,000) to be positioned such that all seven monocolor images are aligned within 20 micrometers of each other.
"Aligning all drums during the print process is an equivalent challenge to parking seven Queen Mary ships to within millimeters of each other," explains Van der Meer. "We brought in mechanical experts to build an accurate frame to hold the drums, but it proved to be economically impossible to achieve the accuracy without an embedded control system."
Because this technique had never been successfully implemented in the industry, the team needed to conduct a feasibility study before developing a real-time prototype of the system.
Solution
Using MathWorks products and training, Océ ensured the feasibility of Perfect Axial Registration by designing, modeling, simulating, and generating code for a real-time embedded control system to align the printer drums. The system consists of two charge-coupled device (CCD) cameras to measure toner markers, seven actuators to position drums, and an optimized control strategy to ensure perfect alignment throughout the process without affecting print efficiency.
To confirm the project’s feasibility, they used MATLAB®, Data Acquisition Toolbox™, Instrument Control Toolbox™, and Signal Processing Toolbox™ to acquire 500x1,000 pixel images from two linear CCD cameras and to develop measurement algorithms that could measure the relative drum positions with micrometer precision.
Researchers used Simulink® and Stateflow® to design, model, and simulate data acquisition, control logic, and actuation prior to hardware implementation.
They then used Simulink Coder™ to translate the high-level control model automatically into low-level C code. Using Simulink Real-Time™, Océ ran the generated code in real time on standard, low-cost PCs to provide a rapid prototype.
"This approach facilitated parallel development by the three team members with much less overhead due to the high-quality code produced by Simulink Coder," notes Van der Meer.
MathWorks products also helped them improve their models quickly. "When we saw something happening in the behavior of the machine, we could adapt the control strategy and change the model very easily," explains Van der Meer. "We did a lot of iterations, but we did them very quickly."
Results
Development time cut in half. "Our three-person team completed a fully functional prototype in just six months with MathWorks tools," explains Van der Meer. "Without these tools, we would have had to extend the project at least by another six months."
Efficiency increased through model reuse. The team has extended the original model for several different printer versions, accelerating the development and testing cycles for new products. "Using Simulink, we created a well-defined structure that enabled us to run the same model on multiple printers. We only have to change one parameter—the machine ID—and the model runs on another machine with different control settings," says Van der Meer.
Learning curve shortened. "We had no previous experience with Simulink Coder and Stateflow," explains Van der Meer. "However, within one to two weeks of taking MathWorks Training courses, we could describe very complex scenarios without any difficulty."
Related Resources